Dòng xe điện thuần đầu tiên của Audi là E-Tron sẽ ra mắt cuối năm nay buộc hãng phải hiện đại hóa lại toàn bộ quy trình kiểm soát chất lượng để đáp ứng lượng linh kiện kỹ thuật số tăng cao.
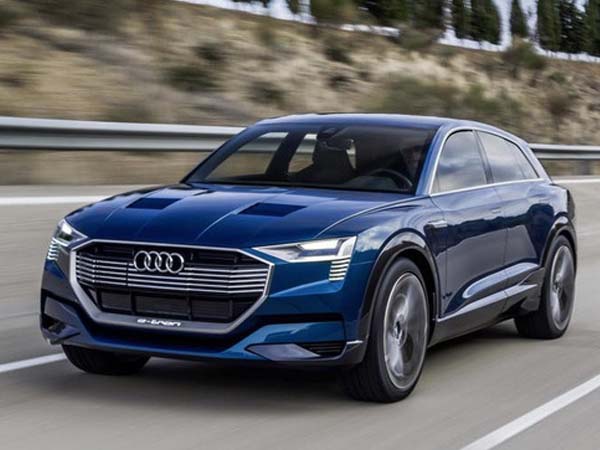
"Audi đang trải qua những thay đổi lớn lao nhất để biến mình trở thành một công ty ô tô với kỹ thuật điện tử hàng đầu. Chất lượng luôn là ưu tiên quan tâm hàng đầu của chúng tôi khi khách hàng luôn mong đợi giá trị, tính năng, độ tiện nghi và bền bỉ hàng đầu từ những mẫu xe của chúng tôi", giám đốc phụ trách chất lượng sản phẩm Audi, ông Werner Zimmermann chia sẻ.
Hiện, toàn bộ phòng, ban liên quan tới chất lượng sản phẩm tại Audi với tổng số lên tới 2.800 người (hầu hết công tác tại trụ sở hãng ở Ingolstadt, Đức) đều đang thực hiện quy trình hoàn toàn mới để có thể thích nghi với số lượng và độ tinh xảo ngày càng tăng của các chi tiết điện tử trên xe.
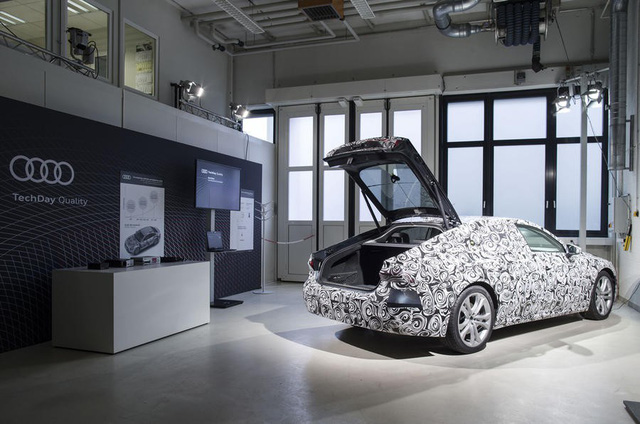
Lấy ví dụ, một dòng xe điện Audi sẽ trang bị hơn 100 nút điều khiển máy tính với khả năng tạo ra 100.000 tín hiệu toàn hệ thống so với chỉ 12.000 tín hiệu trên các dòng xe chạy động cơ đốt trong thông thường ngày nay.
Đội ngũ kiểm tra chất lượng tại Audi thường phụ trách giai đoạn 6 tới 10 tháng cuối cùng của chu trình nghiên cứu và ra mắt sản phẩm (thường là 4 năm) để có thể thay đổi chất lượng xe theo chiều hướng tốt nhất.
Thu hẹp khoảng cách giữa thiết kế và thực hành
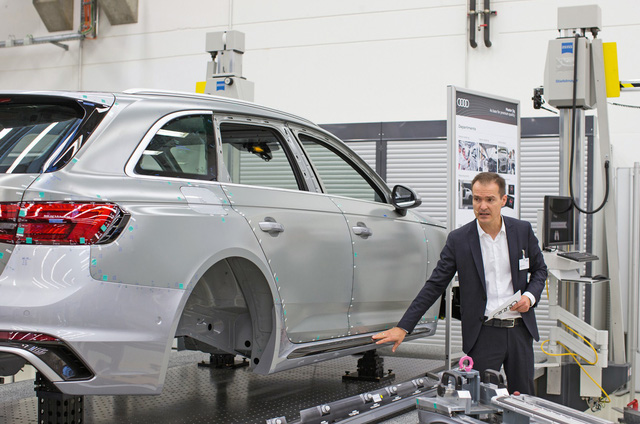
Các công nghệ kỹ thuật số cùng khoa học đo lường đã và đang được Audi ứng dụng tối đa để giảm thiểu sai lệch giữa thiết kế và thực hành.
Hiện tại, hai bộ khuôn mẫu cho ngoại thất và nội thất được chế tạo 10 tháng trước khi Audi đưa xe vào lắp ráp hàng loạt. Các công nghệ chế tác tối tân nhất được áp dụng sao cho sai lệch giữa thiết kế và thực hành lắp ráp được tối thiểu hóa về mức chấp nhận được: 0,2 mm.
Giờ, Audi đang bắt đầu ứng dụng khuôn hỗ trợ quang học, chế tác bởi tay lắp ráp điện tử tự động trang bị 2 camera 16MPM cho phép "dựng" một bức ảnh 3D hoàn chỉnh của khuôn trong 4 giờ. Việc được tái dựng ở cả thực tế lẫn hiện tại cho phép Audi kiểm tra dễ dàng mà chặt chẽ chất lượng khuôn mẫu, từ đó tìm ra điểm sai trong dây chuyền lắp ráp và sửa lại sao cho chặt chẽ, chính xác nhất. Sai số cũng được giảm xuống 1 nửa, còn 0.1 mm.
Thử xe nhanh hơn
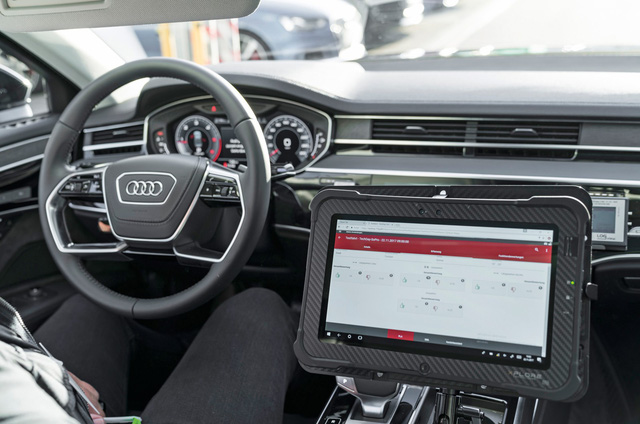
Audi hiện đang cho thử nghiệm E-Tron ngoài đường thực để thu về dữ liệu trực tiếp và chuẩn xác nhất, nhờ đó nhanh chóng phát hiện xem xe có lỗi gì trong vận hành để sửa chữa cả về mặt cơ khí lẫn điện tử. Số xe họ đang chạy thử lên tới... 600.
Chú ý tới từng chi tiết
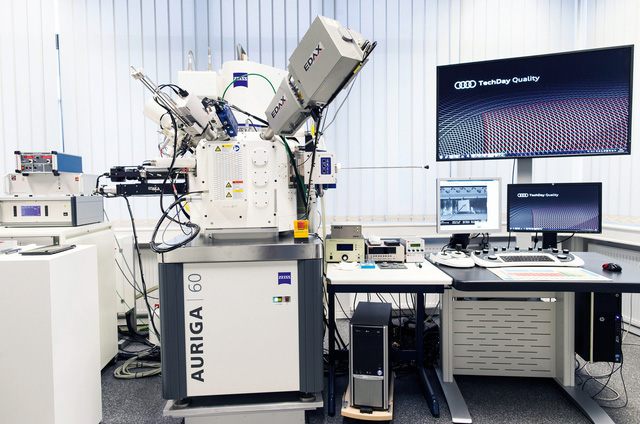
Kính hiển vi điện tử quét tia ion tập trung với giá bán lên tới gần 2,5 triệu USD là trang bị bạn không thường thấy tại các dây chuyền sản xuất xe thông thường. Các chùm tia electron được chiếu vào lớp bán dẫn, sơn phủ, phim xe, vòng bi hay cảm biến, từ đó dữ liệu với độ chính xác 100% về các vật thể dù là nhỏ nhất (5 micromet) được gửi về và phân tích để đảm bảo rằng không có một sai lệch nào xảy ra.
Mới đây nhất, chính thiết bị này đã phát hiện một lớp keo mỏng đã gây ra vấn đề trên màn hình cảm ứng mới của A8 mà hệ thống thông thường không thể phát hiện được.
Tái kiểm tra linh kiện bán dẫn
Chỉ vì dòng xe E-Tron, Audi phải làm lại cả một dây chuyền lắp ráp - Ảnh 5.
Một phòng thí nghiệm riêng được xây dựng để đảm bảo chip điện tử và vi mạch sử dụng trên xe Audi luôn hoàn hảo. Có trung bình 8.000 linh kiện bán dẫn trên mỗi chiếc ô tô ngày nay và 80% trong số các sáng tạo mới trong ngành liên quan tới loại linh kiện này. Số lượng thiết bị qua tay họ kiểm tra ở đây rất đa dạng, từ hệ thống cảm ứng laser LIDAR trên A8 cho tới đèn hậu OLED.